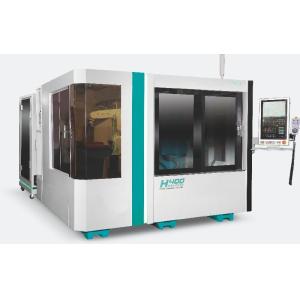
Add to Cart
Inserts grinder H400
1.Adapt to multiple shapes:
Special for hard alloy/ceramic /CBN Grinding of equal material blades.
2.Adapt to the grinding process of blades of different shapes:
(1).This equipment belongs to the four-axis grinding center, which can fully process the periphery, negative chamfering Angle, back Angle and R Angle of the replaceable blade.
(2).The loading and unloading can be realized by the six-axis robot, which can realize the rotation at all angles, reduce the blade turnover process, further improve the efficiency and shorten the grinding time. Automatic clamping, automatic detection, automatic cleaning products, automatic grinding wheel dressing..
(3).Detection function can automatically regrind defective products, and automatically repair the next workpiece.
(4).Independently developed machining simulation software, can effectively prevent misoperation or collision.
(5).Various standard and non-standard cutting tools can be grinding by changing the tooling.
Cutter width | 3 ̴ 15mm |
Thickness | Maximum 20mm |
Length | Maximum 30mm |
C axis positioning accuracy | 0.006deg |
Repeated positioning accuracy of axis C | 0.001deg |
X-axis stroke | 120mm |
Y-axis stroke | 200mm |
Device description:
1. The body and components are cast by Milhanna high grade cast iron FC30, which is artificially normalized heat treatment and then treated by natural aging. Components are processed by YASDA, MITSUI SEIKI, TOSHIBA, ELB and other world-class equipment once clamping processing. Precision size can be up to micron level, to ensure high precision equipment basic components.
2. Machine guide rails and precision ball screws are continuously lubricated by automatic lubrication system to ensure longer service life and accuracy. The cooling system is separated from the body to eliminate vibration and favorable heat dissipation.
3.Equipped with Siemens 828D CNC automatic grinding system, and secondary development, man-machine dialogue fool operation, with many optional equipment to choose from, including inner hole grinding device, automatic end measuring device, automatic outside diameter measuring device, etc.
4. The grinding feed system is composed of a V and a flat track of hand-crafted precision shovel, with automatic lubrication system and C3 level precision grinding ball screw, which can achieve smooth movement, excellent repeated positioning accuracy and long track life.
5. The standard configuration of the grinding wheel spindle is rear four and rear two bearing structure. High precision dynamic and static pressure spindle can also be selected, which has the characteristics of high rotation precision, high dynamic stiffness, good vibration resistance, high grinding efficiency and good grinding surface quality. For special work-piece grinding, the grinding wheel speed can be adjusted, up to 3500 RPM and 60m/s.
6. The tail seat is designed to be both rigid and robust. A hardened alloy steel sliding cylinder encrusted in the cast iron body is designed to carry the MT4 top core. The jacking force of the sliding cylinder can be easily changed by adjustment knobs at the rear. Special accessories oil pressure tail seat with a pedal to facilitate unloading work parts.
7.Siemens numerical control system as the standard configuration, after secondary development, all Chinese operation interface, easy to use. Equipped with Siemens high performance servo motor, the equipment CNC system and drive system have better compatibility, at the same time with automatic sand repair and automatic compensation function, to ensure the stability and precision of feed and grinding.